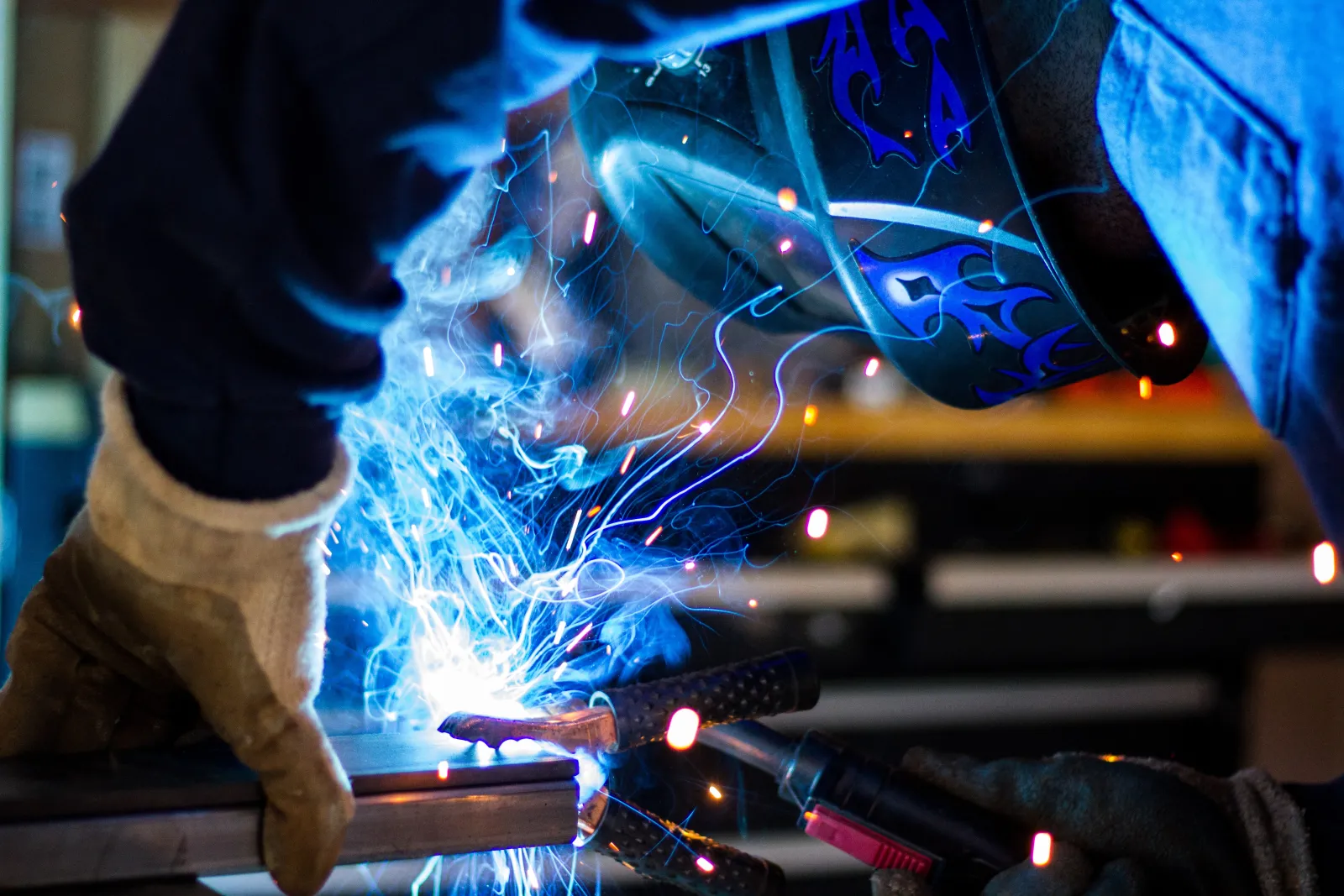
In the specialized world of welding, where sparks fly and metal literally melts, the marriage of artificial intelligence and human craftsmanship is revolutionizing the landscape. "Making Smart Tools Work for Everyone" — one of the Good Systems grand challenge’s six core research projects — is focusing on empowering workers with the aid of smart hand tools and challenging the prevailing narrative of job loss due to automation.
According to a recent Gallup poll, 75% of Americans believe that AI will decrease the number of jobs over the next decade. Kenneth R. Fleischmann, School of Information professor and project lead for "Making Smart Tools Work for Everyone," acknowledges this widespread concern. However, he emphasizes that the goal is not to replace workers but to empower them.
"A human with AI is going to beat either a human without AI or AI without a human."
— Kenneth R. Fleischmann, Smart Tools project lead
“We believe good systems are all about human-AI partnerships,” said Fleischmann. “A human with AI is going to beat either a human without AI or AI without a human. So, that's why our orientation is toward putting the human in control, having the human be the active part of that, and the AI is augmenting a tool that the worker is using, assisting the worker in performing their tasks but not performing the task [for them].”
Melding efficiency with accessibility
The welding profession, known for its inherent risks, poses a unique challenge. Safety data highlight the dangers associated with welding, impacting the attractiveness of the profession as a career choice. The project aims to make welding safer by integrating AI into hand tools, thereby addressing safety concerns and making the workplace more accessible to a diverse range of individuals.
One of the focal points of the project is an augmented reality tool that aids welders in developing muscle memory and transitioning from a virtual to a real-world environment. The simulator serves as a bridge between virtual environments and real-world welding, offering an efficient alternative to traditional training methods. The emphasis is on the worker feeling comfortable and in control, gradually building expertise without the danger of using real tools.
Mechanical engineering doctoral student Carlos Salazar designed the tool, which projects a simulation onto the user’s phone, allowing them to practice techniques and receive instant feedback on their performance (see video below). The simplicity of the design is one key differentiator. In contrast to the industrial-scale models currently on the market, which can cost upwards of $50,000 apiece, Salazar’s app-based version could potentially be manufactured at scale using 3D printers, ensuring it remains affordable — and thus accessible — in the long run.
Demonstration of the prototype. Clip courtesy of Carlos Salazar
“I like how simple it seems to be,” said Troy DeFrates, a former welding instructor and chair of the Welding Technology department at Austin Community College (ACC), and now the interim dean of Design, Manufacturing, Construction & Applied Tech. “I like that it doesn't require a big computer or box or welding machine. I think it's something that a student could use on the weekends or could do at night or at home. We do get asked a lot by students, ‘How can I practice this at home?’ I can see this being good for getting additional practice in, maybe to become aware of certain techniques.”
DeFrates acknowledged the inevitable tradeoffs of training with a simulation. For example, augmented reality will never be able to reproduce the painful experience of being splashed by white-hot drops of welding spatter — and then having to finish the weld without flinching. But as DeFrates pointed out, “I think that’s to be expected, right? It’s not going to be exactly like welding.”
"I like how simple the tool seems to be. I think it's something that a student could use on the weekends or at night or at home."
— Troy DeFrates, Austin Community College
Salazar noted that the current difficulty of handling welding equipment combined with the danger level can turn people away from the field. For example, he described the particular way that the handheld welding tool needs to stay at a precise distance, speed, and angle while wearing the the protective welding helmet, the visor of which blacks out nearly everything.
To achieve optimal results, the project relies on machine learning, which is inherently data-driven. "The first step for machine learning is to collect data,” Salazar said. “AI is always data-hungry. So, the more data that you have, the better accuracy you're going to have in your model."
The project also tackles the physical strain on workers, particularly addressing the concerns of potential workers who might be hesitant to enter the field, such as women and persons who are differently abled. Fleischmann emphasized the importance of making necessary accommodations to ensure a healthy and safe work environment. By utilizing AI ethically, he said, the project aims to create an inclusive workspace that encourages diversity in the welding profession.
Calibration, a laborious aspect of welding, is also targeted for improvement. The setup required for welding, which depends on multiple factors such as metal types and environmental conditions, can be time-consuming. One goal of incorporating AI is to allow welders to create presets, reducing the time spent on calibration and enabling them to focus on the more fulfilling aspects of their job. As Fleischmann put it, "Let AI do what AI is good at. Let humans do what humans are good at and what humans enjoy."
Withstanding the “silver tsunami”
School of Information doctoral student Chelsea Collier, another member of the project team, shed light on the challenges faced by the welding industry, particularly the impending so-called "silver tsunami" as experienced workers with decades of expertise retire. The project recognizes the gap between seasoned professionals and newer workers, who may lack the hands-on experience of their predecessors.
The Good Systems team’s approach ensures that solutions are developed collectively for the benefit of the worker, incorporating insights from both mechanical engineers, computer scientists, and social scientists to avoid surveillance-driven optimization that compromises safety. “What differentiates what we're doing is the participatory co-design,” Collier said. “We're designing with, not for, the user. So it's not about surveillance. It's not about optimizing output at the expense of safety. It's very much the opposite. We're making sure that we are developing this as a collective group of researchers, expert tool users, and novices who want to improve their skills."
"I think what differentiates what we're doing is the co-design. We're designing with, not for, the user."
— Chelsea Collier, Smart Tools project team
Tina Lassiter — another member of the team and a fellow doctoral student in the School of Information — underscored the University’s partnership with Austin Community College as a unique advantage. “Industries have developed their tools with people in academia, along with isolated research they do with students... but we want to look at the real world,” she said. “The (partnership) with ACC gives us a bit of an edge, some unique insights of instructors who have worked as welders and trained future welders.”
ACC’s DeFrates, who has worked extensively with the smart tools team, said that the partnership has been a symbiotic one. “I think they really did a great job trying to get a good, holistic feel for how we all teach — not just one instructor, but multiple instructors. And our students love it. They want to talk about what they're learning. I think it helped them develop the soft skills that a lot of our students don't typically get. So, it's been a pretty good deal for all parties.”